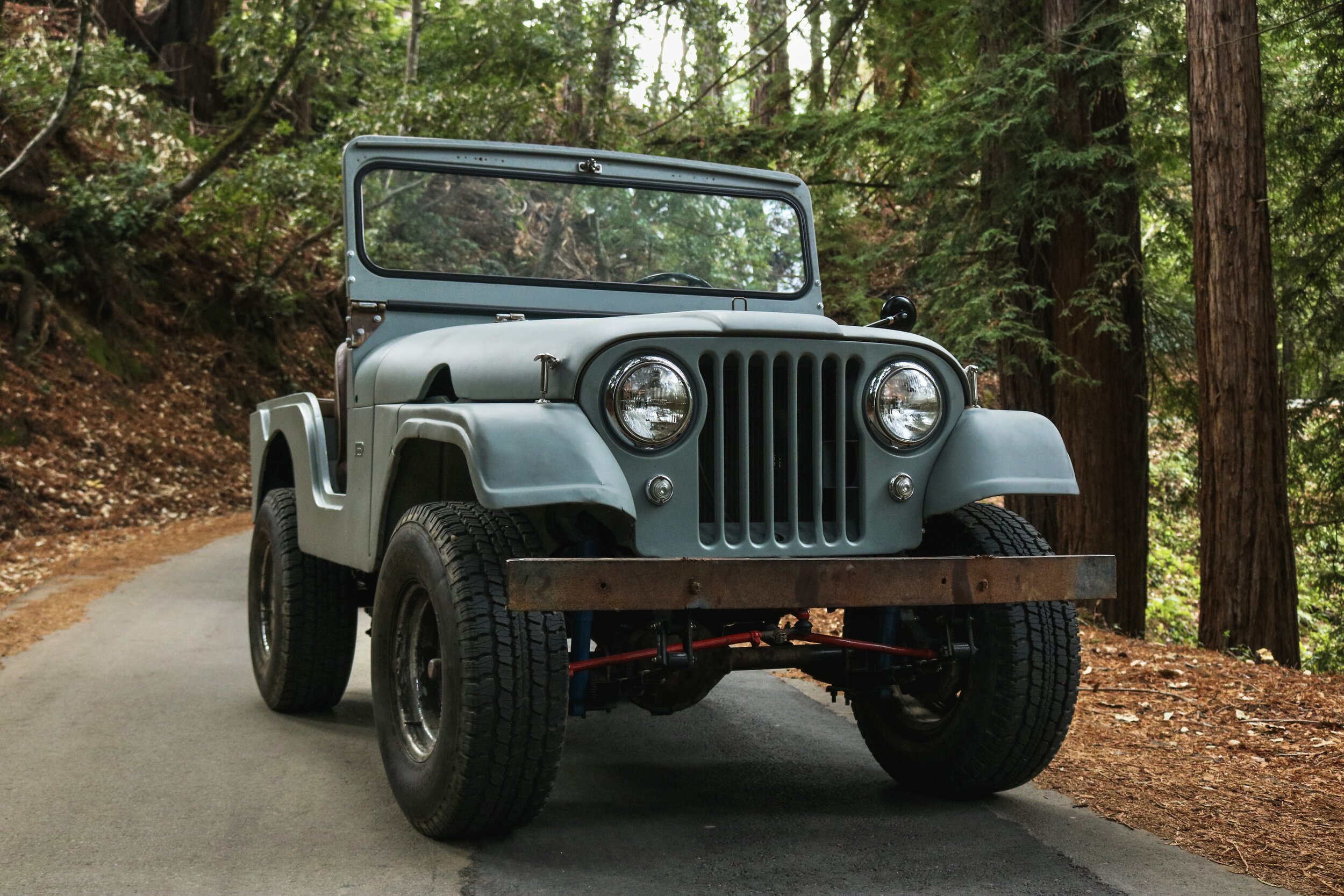
The Jeep
Restoring a 1962 Willys CJ5
2020 quarantine arrived at the end of Spring. Summer jobs are scarce, with minimal socializing. This was the perfect opportunity for a big project, I can recall from the first time I saw a World War II film with an old Jeep bumble around the land scape. I had always wanted one. My sisters were enthusiastic about joining a Jeep restoration team, and played a key role in allowing this huge project happen via convincing my parents to allow this project to happen. Unfortunately, an older Jeep is very expensive, especially for an actual military one. No matter, we decided on a less expensive Vietnam era Jeep, a 1962 CJ5.
Goals
Find a restorable Jeep for $1800
Fully restore for under $6000
Finish all bodywork before school resumes in August
Restore all mechanical components, this includes rebuilding the engine and transmission
Responsibilities
Finding and transporting the project back home
Maintain organization as well as find ways as to not use up too much yard space
Keeping track of costs and knowing when a part should be replaced or renewed
Weighing the benefits of different approaches to fixing something
Timeline
May 2020 - July 2020
What we got to work with
The first picture in this section is the day after we got it, and with the help of some WD40 and tools, we could unfold the layers of this iconic car. What we got can only be reasonably called a pile of rust on wheels. We knew this would be the jeep that we would end up buying due to its lower-than-everyone-else price tag. You can see how collapsed the suspension is, new leaf springs at the minimum will be replaced. We knew it had a seized engine, but had no idea what caused it. I was praying that it would be a piston ring stuck to the cylinder wall, that way I could just free it up, and have an excuse to bore the engine to .030’’ over. Unfortunately this was not at all the source for problems, upon disassembly, we discovered the real cause of the seizure, a spun bearing on rod journal #4. The top-most exposed rod journal in the photo below shows it being very unreflective and very rough and marred. Usually spun bearing failures are caused by lack of oil, lack of oil pressure etc. Basically, there was something wrong with lubrication; maybe it skipped an oil change, and the old oil had lost its viscosity. Maybe the engine became too hot and the oil further thinned. We will never know. I was primarily concerned that this damage raise the possibility of lubrication driven problems in multiple areas. Fortunately the only other damage in the engine was slight scoring on cylinder #4, but this could easily be corrected with a hone.
After I inspected the camshaft, I decided that even if I wanted to change it along with the lifters or pushrods, I couldn’t afford it. Keep in mind that this engine is nearly the same as the military engine, so it will run on just about any quality of gas and oil. To further illustrate it’s design for reliability and sustained operation, it redlines at just 4000 rpm’s. The reason for such a low redline is due to its long stroke length, which translates into more torque. This engine design prioritizes reliability over performance. The pistons, cam shaft, valves, rockers and so on looked like they were in good condition. However, the crankshaft damage required repair at the machine shop. Material had to be welded on and ground back down smooth to make up for the material lost due to the spun bearing. A very similar decision was made for the connecting rods; they were measured, and ground to size. All new connecting rod and main bearings were put in, all .015’’ undersized. With new bearings, and assembly lube, I plasti-gauged the tolerances, and everything was torqued down to spec. We gave the block a nice coat of “high-heat“ paint, and red on the valve cover to add some flair.
Some extra info about this engine
The keen eyed reader will notice that this engine has overhead valves and at the same time is a flat head. This is unusual, and the very original WWII engine was completely a flathead that produced about 60 hp. The Willys Jeep engineers did some experimenting, and found that by making the intake an overhead design, while keeping the exhaust a flat head, there was a gain of power to about 70 hp. It seems marginal, but it was very clever nonetheless. If you look closely, specifically on piston #1, you can see 06 stamped on the top. This indicates .060’’, which means that the block had previously been bored sixty thousandths oversized. This also means that this engine had been taken apart and worked on since 1962, and the very clean looking pistons and fairly distinct hatch marks from a past hone make me believe that this had been a recent job.
Body Work
This Jeep was kept outside, and was used to transport salt to cows. The tub of this Jeep was thus very rusty, with holes larger than a piece of printer paper. The options were either to buy a new tub (body), or to patch the holes. I was not confident in repairing the tub in its state, nor did I believe it to be worth the effort. I searched Craigslist for another Jeep tub, found one for $350, and talked the seller down to $300. The adjacent photo is the back right of the “new” tub, where the old spare tire was mounted. There was some sheet metal weakened by rust remaining, but it was less than 2mm thick before I even started wire brushing the rust away. This called for the replacement of sheet metal, which was welded in. There were several little dents all over the tub which got filled in with body filler before primer and paint.
We decided to paint the Jeep a semi gloss Naval Grey, one of the regulation military colors.
After the primer was sprayed on, the dents and low spots seemed to disappear.
This is a review of the entire very economical painting process. We bought a $15 paint spray gun from Harbor Freight, and utilized 2 small compressors in parallel to make sure there was enough flow at a high enough pressure.(painting an entire car requires a lot of air). The booth itself was a wooden cube frame using salvaged lumber, dressed with painters plastic, built inside a friends garage. It was fully enclosed and had a box fan acting as a method of ventilation. A reason for building this booth inside a garage for temperature control. This garage method was the best option. All the different parts of the body (the tub, the left fender, right fender, grill and hood) were painted individually in the smaller space.
A side angle shot below reveals the “far from good, but good from afar” paint job we created. It’s a Jeep; I assume some mud will later hide its imperfections. Safety was important in this enclosed space, spraying paint mixed with paint thinners is very hazardous. An N95 Home Depot mask is useless for this sort of painting. A mask with filters than can handle the organic solvents is required, as shown worn in the picture below. A painting suit helps avoid ruining your clothing, and old shoes are a must.
After the main tub was painted, all other small body panels such as the dashboard, grill and steering column were painted. Once all parts dried we were ready to bolt the Jeep back together.
Chassis Repairs and Servicing
In this here photo you see me teaching my sister to weld. There were a few cracks in the frame. After drilling a hole at the end of the cracks we laid down a weld bead (no concentrated stress point in a circle). Additionally we performed a complete rust removal using concrete etcher. This was necessary before we undercoated the frame, top and bottom. With the engine removed, it was a golden opportunity to check the transmission. The previous owner had told me that the transmission had a tendency to pop out of second gear while decelerating. For anyone curious, this is the most common problem with older Jeeps. It is caused by the following: the second gear is a helical gear, and under a change of angular velocity, the helical gear either “tightens” and pulls second gear more solidly in the transmission, or “loosens” and pops the synchro mesh shifter unit out of gear and into neutral. This is a sub optimal design, but these transmissions are overbuilt and have good support in terms of aftermarket parts and community knowledge.
I was told that new synchros (little friction rings that synchronize the different shafts in the transmission to the same speed during shifts for smooth changes) fix the popping-out-problem, While I was working on the transmission, I checked the wear on the teeth of the gears, as well as replace old gaskets.
Some additional items that were not mentioned: I replaced all leaf springs and bushings involved in the Jeeps suspension, all axle U-bolts attaching the solid axles to the leaf springs were replaced, as the old ones snapped during disassembly and were severely stretched out.
With the engine reinstalled, transmission filled with oil, and the radiator bolted in place upfront, we were ready to idle the whole frame to my friends house, where the body and interior pieces were being kept.
At this stage we can now start the final assembly process.
Assembly Time!
The beauty of the Jeep design is that the body is completely independent of the frame. This allows assembly as well as disassembly by one or two people. Once the tub was set on top of the frame, I could go around to each of the mounting holes, and insert a rubber spacer (to prevent rattling) between the body and frame. Only eight 5/8’’ bolts holds the entire body down; one for the grill, none for the fenders, and seven for the tub.
This is a top view of the assembly process. You can see how everything fit together without the fenders on. There are several cables going entering the firewall (front of the tub). These wires and cables from left to right are, the speedometer cable, distributor +12v power wire, alternator charging indicator wire, the +12v solenoid starter wire, and at the far right of the picture, the parking break cable.
The wiring for this car is very simple. There is no factory installed fuse box, the only protection the whole car has is a 20 amp breaker between the ignition switch and all the electronics that are fed from said ignition switch. I thought about putting in my own fuse box, but that would have doubled the wiring needed, and furthermore the wiring is so simple, there are so few things to go wrong, that it is hard to justify the extra effort and expense. Even if there were an electrical fire, there would be nothing to burn, as the Jeep is made completely of steel.
The photo to the left shows the Jeep only partially bolted together. With a 5 gallon bucket for a seat, I was to test drive it, looking for problems that had to be fixed before the fenders went on. Or worse, the engine had to come out. It was concluded that the rest of the assembly could continue. The engine ran strong, and if its not a cold winter day, it starts right up and immediately builds oil pressure. Nearly a year after completion, the engine runs as well as it did the day it was finished.
The final steps were mounting the seats, fenders, hood, windshield and tailgate.
The biggest concern that is most certainly warranted is the lack of seat belts. The car never came with them from the factory and is therefore exempt from legally requiring them. A second great concern is the lack of a roll cage, and a canvas top for sun protection. These will be added when time permits, as currently I am still in college and the car is back in California. Hopefully between the school year ending and co-ops I can add the protective measures this Jeep needs.
Learnings
This whole project was a learning process. Every turn in the project revealed something that I had never worked with before. I had taken auto shop in high school and worked on mechanical things in my free time. I had assumed that I would know everything needed for this job. A single problem in this projects introduced several more problems required to address the initial one. An example of this was removing the engine from the frame for the rebuild. How in the world was I going to lift a 400lb block of iron? I do not see myself frequently lifting engines, we do not have the standard equipment for lifting engines. We do not have a lot of storage space, so an engine hoist or cherry picker was not at all justifiable. What I ended up doing was buying a cheap block and tackle pulley with a 5:1 reduction. With the help from my sisters, we were able to hoist the engine out, and onto an engine stand to begin the rebuild. I learned about the several tolerances throughout the crankshaft. The unusual oiling system and the reasons for certain designs made were all revealed by working on it, blowing on tubes and turning the engine over without the valve cover. Rebuilding this simple 3 speed transmission was incredible, I got to see the issues faced by engineers at the beginning of the century, and the solutions that were found to solve those issues ( the transmission design is from the 1930’s). The whole painting process was completely new to me. Prior to this I had never held a paint gun or done serious paint mixing or preparation. I now have one cars worth of practice. At the end of this all, I am certain that I learned why mechanics, painters, engine rebuilders and machinists charge the amount they do. It is genuinely hard work and getting it done fast is no easy feat. I was impressed that I was able to enjoy the Jeep for two and a half weeks before I had to had back to RIT.